SMART FACTORY
Le projet de la Smart Factory vise à la production 100% autonome de différents objets.
Ici, les objets en question sont des badges munient d’un tag RFID ou d’un autre d’une clé USB ou encore d’un jeton de Caddie. C’est ces éléments qui seront produits par la Smart Factory. Allant de la création du boitier jusqu’au stockage du produit fini en passant par un assemblage automatisé et diverses autre tâches de production.
La Smart Factory est composée de multiples cellules robotisées.
Chacune de ces cellules se voient amener les éléments dont elles ont besoin grâce à la cellule mobile. Ensuite, elles effectueront les tâches de production leurs étant attribuées.
Ce qu’il faut retenir est que la cellule mobile est l’outil le plus important de la Smart Factory, car c’est elle qui a pour mission de transporter les diverses pièces et produits finis.
Chacune des cellules est munie d’un serveur OPC UA permettant ainsi l’échange d’informations de façons optimales.
Chaque cellule mettra à disposition des informations de production et écoutera en permanence l’API maître qui lui indiquera ce qu’elle a faire.
Ces serveurs permettent aussi d’établir des diagnostics de maintenance automatique accessible à distance par le personnel concerné simplifiant ainsi les opérations de maintenance sur les diverses cellules de la Smart Factory.
CELLULE STAÜBLI
Le projet de la cellule staübli consiste à simuler la production de pièces industrielles à l’aide de billes. C’est le robot qui se charge de les placer dans les machines permettant d’effectuer la production.
Les billes sont ensuite placées dans des palettes étant remplies chacune leur tour au fur et à mesure de la production. C’est aussi le robot qui est responsable de prendre une palette vide, de la remplir de billes et lorsque celle-ci est pleine, il doit les placer dans l’empreinte « palette » pleine ».
Cette cellule est un bel exemple de ce que peut faire le technicien ES en sytsèmes industriels. Dans ce projet, nous pouvons y trouver de la CAO, de la robotique, de la pneumatique, de la sécurité de machine ainsi que de la programmation automate qui permet le pilotage de l’intégralité des éléments constituant cette cellule.
Au fur et à mesure des années, plusieurs étudiants ont travaillé sur cette cellule. Elle comprend de nombreuses améliorations et correctifs permettant de la rendre de plus en plus efficace.
Conception CAO
De multiples éléments CAO ont été conçus par les étudiants de l’ES. En voici les principaux :
Robotique
La cellule est équipée d’un robot industriel de la marque Staübli. Afin de le faire fonctionner, les étudiants ont utilisé le logiciel de programmation adapté afin de prendre les positions de celui-ci et d’établir une communication avec l’automate maître de la cellule.
Sécurité
Le robot étant industriel, en temps normal, une cage complètement fermée aurait été de mise. Cependant, cette cellule peut être en partie ouverte grâce à la présence d’un analyseur d’environnement de chez SICK.
Dans le cadre de ce projet, ce dispositif, placé dans un angle de la cellule, est utilisé pour délimiter deux zones. La première étant une zone de ralentissement du robot et la seconde (celle étant la plus proche de la cellule) arrête le robot.
L’analyseur est autonome par rapport à l’automate maître, il vient se brancher sur le contrôleur du robot et communique directement avec lui.
Ceci permet, comme mentionné plus tôt, de faire travailler le robot avec une cellule partiellement ouverte. Permettant, lorsqu’un problème survient, aux personnes concernées de se rapprocher de la cellule sans risque et y appliquer les correctifs.
CELLULE MOBILE
Organe le plus important de la Smart Factory. Comme son nom l’indique, elle est mobile. Cette cellule a été mise en place pour effectuer des transports de matériaux de façon autonome dans les diverses cellule de l’industrie 4.0.
CAO
La partie CAO a été faite en collaboration avec les automaticiens CFC pour le châssis ainsi qu’avec les dessinateurs en microtechnique CFC pour l’habillage de la cellule mobile.
Un autre élément CAO tout aussi important est la partie « docking » du projet. Il s’agit de l’endroit auquel le MIR vient s’amarrer lui permettant un accès au 230V et à de l’air comprimé.
Robotique
La concernant, elle possède deux robots, l’AVG de chez MIR permettant à la cellule de se déplacer ainsi qu’un robot CRX-10 de chez FANUC monté sur le dessus permettant l’interaction et le transport d’éléments provenant des diverses cellules.
L’AVG de chez MIR possède des scrutateurs lui permettant de cartographier la zone pour se déplacer. Il fut nécessaire d’effectuer une cartographie générale de la pièce. Cette même carte a été configurée pour déterminer l’emplacement des « docking » prévu pour le MIR.
Automation
L’intégralité de la cellule est commandée par un automate de chez Beckhoff. C’est lui qui ordonne à la cellule de se diriger aux emplacements désirés et qui dit quoi faire au robot à l’aide de diverses communications représentées par le schéma de principe ci-contre.
CELLULE « LINETRACKING »
La cellule « LineTracking » permet de récupérer des objets sur une bande en mouvement à l’aide d’un robot collaboratif de chez Fanuc et d’ainsi de placer ces objets dans les compartiments adéquats.
Concernant cette cellule, plusieurs aspects de la formation y ont été appliqués. Notamment de la CAO, de la robotique et de l’automation.
CAO
Projet de module CAO visant à l’ajout d’une seconde bande pour le stockage des boîtes de montres.
Projet contenant de l’assemblage d’éléments provenant de divers fabricants ainsi que de création CAO fait par l’étudiant en question (3.2.2, 3.2.3)
Robotique
Concernant la partie robotique, un robot collaboratif de chez Fanuc a été utilisé.
Celui-ci, à l’aide de son contrôleur pourvue d’une carte supplémentaire, est utilisé pour la récupération des pièces se trouvant sur la bande. Il allie à la fois de l’analyse d’images à l’aide d’une caméra se trouvant au début de la bande permettant de déterminer sur quel hauteur de l’axe Y la pièce se trouve ainsi qu’un nouvel axe fourni par la carte supplémentaire permettant de déterminer la position de la pièce sur l’axe X.
Le tout est ensuite cindé en un seul programme permettant l’exécution de cette tâche.
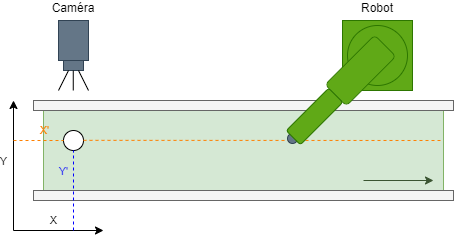
CELLULE SCARA
La cellule Scara est un projet permettant le gravage de diverses pièces. Actuellement, celle-ci grave des kaplas ou des puzzles.
Concernant cette cellule, plusieurs aspects de la formation y ont été appliqués, notamment de la CAO, de la robotique et de l’automation.
CAO
Concernant une partie de la CAO, le but était d’automatiser la porte de la graveuse. Pour ce faire, la graveuse a été modifiée pour accueillir un système de poulies.
Robotique
Concernant la partie de robotique, l’objectif fut d’utiliser un robot collaboratif SCARA de chez Dobot. Ce robot se programme en Python et échange des informations avec l’automate à l’aide d’une communication TCP/IP. Cette communication permet à l’automate de donner les ordres au robot.
La mission de celui-ci est de placer les éléments devant être gravés dans l’empreinte placée sur l’axe linéaire FESTO qui sera chargé d’amener les pièces à l’intérieur la graveuse.
Automation
En soit, il faut se fier au PLC Wago, c’est lui qui gère l’intégralité de la cellule. Il communique avec un IPC Beckhoff qui permet de piloter la graveuse et le moteur de la porte. De plus, l’automate communique en TCP/IP avec le robot, lui permettant de lui donner les ordres.
La partie automation de cette cellule est représentée par ce schéma :
API MAÎTRE SF
Le projet de l’API maître consiste à la gestion de l’industrie 4.0. C’est elle qui donne à toutes les cellules leurs missions.
Il s’agit d’un projet purement Software. Un pc industriel Beckhoff muni d’un serveur MODBUS a été utilisé pour mettre à bien ce projet. Le serveur en question est implémenté sur le PC industriel. Chaque cellule de la Smart Factory peut lire et écrire dans ce serveur. Le PC industriel récupère ces données et change la valeur de certains registres du serveur permettant de donner les ordres aux diverses cellules.
La façon dont est donné les ordres est fait de deux méthodes. La première consiste à l’utilisation d’une reconnaissance vocale codée en C# et la seconde consiste à l’utilisation de SMS envoyé sur une passerelle qui retranscrit l’ordre en UDP sur l’API maître. Que ce soit par SMS reconnaissance vocale, les ordres sont les mêmes. De plus, la partie SMS permet d’avoir le statut de l’usine et ainsi de savoir ce qu’il se passe même lorsque l’utilisateur n’est pas sur place.

Voici deux vidéos représentant l’API maître en action :